By Kenney Kost/editor-in-chief
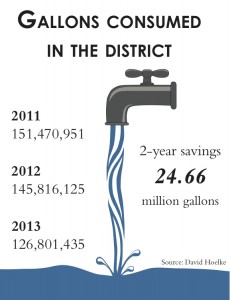
TCC is implementing a plan to reduce energy and utility costs by $850,000-$2.25 million per year through conserving water and energy.
Currently, the college spends $8.52 million on energy and utilities — the second-largest budget expenditure for the district.
Operational infrastructure director Walter Williams said his team has identified roughly $125 million in repair and update needs throughout the district in regards to energy and utilities.
“Within that, some of those needs will bring savings to the district,” Williams said. “About $40 million of that has a payback.”
Some of the plan has been implemented and is already achieving a considerable amount of success, particularly in the area of water conservation, Williams said.
Director of systems infrastructure utilities and energy David Hoelke said the college could save water in a number of ways. Things like running water faucets are a major area of concern.
“In today’s world for water conservation, you look at fixture flow rates,” Hoelke said. “With typical lab fixtures today, there are restrictors to hold it to a half gallon a minute versus one-and-a-half to two gallons a minute before. And now, most of our fixtures have occupancy sensors.”
Hoelke said the same thing applies with regard to urinals and toilets. Old urinals use about three gallons per flush, and TCC’s urinals are down to one-eighth gallon per flush. Old toilets use about three-and-a-half to four gallons per flush, and TCC’s toilets are down to 1.28 gallons per flush, Hoelke said.
Over the last two fiscal years, TCC has saved 24.66 million gallons of water and has won the City of Fort Worth’s Smart Water Conservation Award twice.
Continuous commissioning is another area TCC is working to improve, Williams said. TR Campus has a lighting and heating, ventilation and air conditioning control system.
“Basically, it’s those controls, thermostats and the stuff upstream of that and optimizing the way all of that operates and turning it off when you don’t need it,” Williams said.
Hoelke said this all ties into the energy measurement and verification system TCC is in the process of implementing.
“What it amounts to is we measure the electrical energy, the BTUs for heating and cooling, and, where it’s appropriate, we measure the amount of natural gas and the amount of water going into our buildings,” he said.
With these measurements, Hoelke said TCC can develop baselines.
“Then you can go building by building and compare these baselines with what groups like the Texas A&M energy services lab have compiled from thousands of educational facilities,” he said. “And they can say you’re not achieving what you should or you are.”
Over the next five to seven years, Hoelke said, the country will completely transition to LED lighting, and TCC has roughly two million square feet of lighting to replace.
“A well-designed LED fixture will operate around 100,000 hours versus the old lamp changeouts being about 40,000 to 60,000 hours with a list of fine print to actually achieve those numbers,” he said.
Hoelke said TCC has already dropped its kilowatt-per-hour charge by 50 percent.
“That is the part that is a competitive commodity, meaning cost from the energy company,” he said. “It’s [the savings] from using good competitive process and also the fact that there is an abundance of natural gas available at the moment.”
Williams said TCC recently joined the City of Fort Worth’s Better Buildings Challenge to let the public know TCC is practicing good environmental stewardship.
“It’s a recognition thing,” he said. “It’s to document the things we would be doing anyway and puts it in that forum to give us some publicity and get the word out about what we are doing.”